パッケージの技術開発で業界を牽引してきたキリンビールは、2008年、製造業で第1号となるエコ・ファースト企業に認定された。そして今年、炭酸飲料向け330ミリリットルワンウェイびんとして「これまでの国内最軽量」を更新した「グランドキリン」を発売する。パッケージの軽量化を通して、環境負荷軽減に挑戦し続けるキリンビールの取り組みを紹介する。
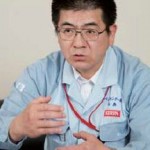
キリンビールは、ビール・発泡酒、清涼飲料などの容器包装やパッケージング技術の開発を行うパッケージング技術開発センターを自社で有している。一般的に、飲料メーカーは、製品に使用する容器を自社で製造しないため、同様のセンターを保有する飲料メーカーは少ないという。
これまでパッケージング技術開発センターは、1980年代前半の小容量炭酸飲料用ペットボトルや軽量リターナブル大びんなど、時代に先駆けて環境に配慮したパッケージを次々と開発してきた。
パッケージング技術開発センターの松島康之センター長は「重要なのは中身であって、お客様は容器を買っているわけではありません。我々は、容器にかけるコストは低くするべきだと考えています。そのために、より利便性が高く、より軽く、より素材の使用量が少ないパッケージを追求してきました。その取り組みが環境負荷の軽減にもつながっているのです」と語る。
◆独自の技術で最軽量を実現
容器軽量化の第1号となったのは、1993年に導入された国内最軽量のリターナブル大びんだ。
「重量規制により、当時はトラックに大びん製品を満杯に詰め込むことができなかった。満杯に詰み込むことができるレベルまでびんを軽量化しようというのが、きっかけでした」
開発に携わった小田朝巳は、軽量リターナブル大びんの開発に至った経緯を振り返る。軽量化を可能にしたのは、キリンビール独自のコーティング技術だ。びんの外表面に約0・1マイクロメートル (マイクロメートル=1/1000ミリメートル)のセラミックコーティングを施すことで、強度を確保しながら約21%軽量化し、国内最軽量を実現した。これにより、2011年までに原材料を5万5千トン、LCA -CO2排出量を5万7千トン削減することができた。
競合メーカー3社とキリンビールのリターナブルびんを比べてみると、キリンビールのみ形状が異なり、肩の部分にロゴマークの型押しが入っている。他社は、びんを共有しているが、キリンビールは自社専用のびんを使用しているためだ。
専用びんを用いるのは、「軽量化の開発に対してコストをかけることができるため」だという。一方、アルミ缶についても1994年に国内でいち早く小口径アルミ缶を導入し、キリンビールが蓄積した技術ノウハウを競合メーカーと共有することで、ビール業界・製缶業界におけるアルミ使用量とCO2排出量削減に貢献した。
また2011年には、業界に先駆けて、さらに約1グラム軽量化した国内最軽量のアルミ缶の採用を全工場で開始した。